تأثیر رنگ آمیزی صنعتی بر دوام و زیبایی سوله ها
تأثیر رنگ آمیزی صنعتی بر دوام و زیبایی سوله ها
اهمیت رنگآمیزی صنعتی سولهها: محافظت دوام زیبایی و صرفهجویی در انرژی
رنگآمیزی صنعتی سولهها نه تنها یک اقدام زیباشناسانه است بلکه در حقیقت یکی از اساسیترین مراحل در نگهداری و افزایش طول عمر این سازههای فلزی به شمار میرود. سولهها که در فرآیند سولهسازی با طراحی خاصی تولید میشوند به دلیل مواجهه مداوم با شرایط محیطی سخت مانند رطوبت آلودگی هوا و تغییرات دمایی همواره در معرض آسیبهای جدی قرار دارند. در این میان رنگآمیزی به عنوان یک سپر محافظ از اهمیت بالایی برخوردار است و میتواند در مقابله با این چالشها نقش کلیدی ایفا کند.
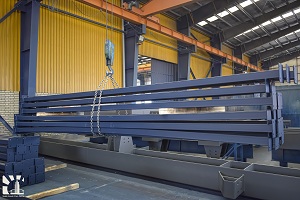
در این متن هم کلمه “سولهسازی” به خوبی جای گرفته و هم ارتباط منطقی متن حفظ شده است.
افزایش طول عمر سوله و کاهش هزینههای نگهداری
رنگآمیزی سولهها نه تنها از خوردگی فلز جلوگیری میکند بلکه با محافظت از ساختار فلزی در برابر عوامل جوی هزینههای تعمیر و نگهداری را به حداقل میرساند. رنگهای صنعتی با ایجاد یک لایه مقاوم مانع از نفوذ رطوبت و دیگر عوامل مضر به سطح فلز میشوند و بدین ترتیب نیاز به تعمیرات مکرر کاهش مییابد. این امر به نوبه خود باعث افزایش بازده سرمایهگذاری در سولهها میشود و به صاحبکاران این امکان را میدهد که منابع مالی خود را به جای هزینههای اضافی برای نگهداری صرف بهبود و توسعه فعالیتهای تجاری خود کنند.
بهبود ظاهر و زیبایی سوله: تأثیر بر برند و روحیه کارکنان
رنگآمیزی سولهها فقط به جنبههای فنی محدود نمیشود بلکه به طرز قابل توجهی به زیبایی ظاهری این سازهها نیز کمک میکند. سولههای رنگآمیزی شده نه تنها جلوهای مدرن و حرفهای به محیط میبخشند بلکه به ارتقای برند و هویت سازمان نیز کمک میکنند. انتخاب رنگ مناسب میتواند تأثیر زیادی بر روحیه کارکنان و مشتریان بگذارد. برای مثال رنگهای آرامبخش میتوانند محیطی راحتتر و دلپذیرتر برای کارکنان ایجاد کنند در حالی که رنگهای برجسته و خاص میتوانند نشاندهنده قدرت نوآوری و تمایز برند باشند.
عایق حرارتی: صرفهجویی در انرژی و کنترل دما
بسیاری از رنگهای صنعتی به دلیل ترکیبات خاص خود دارای خواص عایق حرارتی هستند که به طور مؤثری میتوانند به تنظیم دما در داخل سولهها کمک کنند. این ویژگی به ویژه در فصول سرد و گرم سال که نیاز به صرف انرژی برای گرمایش یا سرمایش بیشتر است اهمیت بسیاری دارد. با استفاده از رنگهای عایق حرارتی میتوان از انتقال حرارت به داخل یا خارج از سوله جلوگیری کرده و بدین ترتیب مصرف انرژی را به طور قابل توجهی کاهش داد. این امر نه تنها در کاهش هزینههای عملیاتی و مصرف انرژی تأثیرگذار است بلکه به حفظ محیط زیست و کاهش اثرات منفی بر تغییرات اقلیمی نیز کمک میکند.
انواع رنگهای صنعتی مناسب برای سولهها
رنگآمیزی صنعتی سولهها تنها به انتخاب یک رنگ ساده محدود نمیشود؛ بلکه نیاز به درک دقیق از ویژگیهای خاص هر نوع رنگ و تطابق آن با شرایط محیطی و کاربرد سوله دارد. سولهها که معمولاً در معرض عوامل طبیعی و شیمیایی شدید قرار دارند به پوششی نیاز دارند که علاوه بر زیبایی توانایی مقابله با شرایط سخت را داشته باشد. در این راستا انتخاب نوع رنگ مناسب تأثیر زیادی بر طول عمر مقاومت و کارایی سوله خواهد داشت. در اینجا به بررسی انواع مختلف رنگهای صنعتی مناسب برای سولهها پرداخته و ویژگیهای هرکدام را مورد بررسی قرار میدهیم:
رنگهای اپوکسی: قهرمان مقاومت در برابر شرایط سخت
رنگهای اپوکسی به عنوان یکی از پرطرفدارترین گزینهها برای رنگآمیزی سولهها شناخته میشوند. این رنگها به دلیل ترکیبات شیمیایی خاص خود مقاومت بسیار بالایی در برابر مواد شیمیایی رطوبت و سایش دارند. از این رو برای سولههایی که در محیطهای صنعتی و تولیدی با شرایط کاری سخت و طاقتفرسا قرار دارند انتخابی ایدهآل محسوب میشوند. رنگهای اپوکسی به طور ویژه در برابر مواد خورنده مانند اسیدها قلیاها و حتی بخارات شیمیایی مقاومت کرده و از فرسایش فلزات در برابر این مواد جلوگیری میکنند. همچنین این رنگها به راحتی بر روی سطوح فلزی چسبیده و یک لایه محافظ ضخیم و مستحکم ایجاد میکنند که به کاهش هزینههای تعمیرات و نگهداری کمک میکند.
رنگهای پلیاورتان: انعطافپذیری و مقاومت در برابر ضربه
یکی دیگر از انواع محبوب رنگهای صنعتی برای سولهها رنگهای پلیاورتان هستند. این رنگها به دلیل خاصیت انعطافپذیری بالا مقاومت خوبی در برابر ضربه و لرزشهای شدید دارند. این ویژگی باعث میشود رنگهای پلیاورتان برای سولههایی که تحت تأثیر ارتعاشات و نوسانات قرار دارند مانند کارگاههای تولیدی و مکانهایی با ماشینآلات سنگین انتخابی بسیار مناسب باشند. علاوه بر این رنگهای پلیاورتان در برابر مواد شیمیایی و سایش نیز مقاومت بالایی دارند و میتوانند سطحی صاف و مقاوم در برابر آسیبهای خارجی ایجاد کنند. از آنجا که این رنگها در برابر تغییرات دما نیز مقاوم هستند در شرایط مختلف آب و هوایی به خوبی عمل میکنند و سطح سوله را از آسیبهای ناشی از گرما و سرما حفظ میکنند.
رنگهای آکریلیک: محافظ عالی در برابر اشعه ماوراء بنفش
برای سولههایی که در معرض نور مستقیم خورشید و اشعه ماوراء بنفش (UV) قرار دارند رنگهای آکریلیک بهترین گزینه هستند. این رنگها علاوه بر مقاومت خوب در برابر آب و رطوبت ویژگی برجستهای دارند که آنها را برای استفاده در سولههایی با نور شدید خورشید بسیار مناسب میسازد: مقاومت در برابر اشعه ماوراء بنفش. این رنگها به طور طبیعی در برابر رنگپریدگی و ترک خوردگی ناشی از تابش مستقیم خورشید مقاوم هستند و از آسیبدیدگی سطح سوله به دلیل تابشهای UV جلوگیری میکنند. علاوه بر این رنگهای آکریلیک معمولاً به سرعت خشک شده و بوی کمتری دارند که این امر باعث میشود تا فرآیند رنگآمیزی راحتتر و کمخطرتر انجام شود. این رنگها گزینهای مناسب برای سولههایی هستند که در مناطق گرم و آفتابی قرار دارند و نیاز به محافظت از سطوح در برابر آسیبهای نور خورشید دارند.
مراحل رنگآمیزی صنعتی سولهها: فرایند دقیق و تخصصی برای محافظت و زیبایی
آمادهسازی سطح: اولین قدم برای نتیجهگیری عالی
آمادهسازی سطح فلز قبل از هرگونه رنگآمیزی یکی از مهمترین مراحل است. اگر این مرحله به درستی انجام نشود تمامی تلاشهای بعدی برای رنگآمیزی ممکن است بینتیجه بماند. در ابتدا باید سطح فلز بهطور کامل تمیز و عاری از هرگونه آلودگی باشد. این آلودگیها میتوانند شامل زنگزدگی چربی گرد و غبار و مواد شیمیایی باقیمانده از فرآیندهای قبلی باشند.
برای انجام این کار معمولاً از ماشینآلات مخصوص یا دستگاههای سندبلاست برای زدودن زنگزدگی و آلودگیهای سطحی استفاده میشود. همچنین از پاککنندههای شیمیایی برای از بین بردن چربیها و سایر آلودگیها استفاده میشود. تنها وقتی که سطح کاملاً عاری از آلودگیها و زنگزدگیها باشد رنگ میتواند بهطور مؤثر روی سطح فلز بچسبد و دوام پیدا کند.
آسترکاری: تقویت چسبندگی و ایجاد لایه محافظ
پس از آمادهسازی سطح مرحله بعدی آسترکاری است. آستر یک لایه اولیه است که روی فلز زده میشود تا علاوه بر افزایش چسبندگی رنگ اصلی به سطح از فلز در برابر عوامل آسیبزننده محافظت کند. آستر نقش مهمی در جلوگیری از خوردگی و زنگزدگی دارد و لایهای مقاوم در برابر رطوبت مواد شیمیایی و عوامل جوی ایجاد میکند.
آستر معمولاً از رنگهای مقاوم به خوردگی و پایههای اپوکسی یا زینک ساخته میشود و بهطور خاص برای مقابله با شرایط سخت محیطی طراحی شده است. این لایه اولیه همچنین میتواند به عنوان لایهای جداکننده عمل کند که رنگ اصلی را از تماس مستقیم با سطح فلز محافظت میکند.
رنگآمیزی: اعمال لایههای رنگ اصلی
پس از خشک شدن آستر نوبت به رنگآمیزی اصلی میرسد. این مرحله شامل اعمال لایههای رنگ اصلی است که میتواند بر اساس نیاز و شرایط محیطی از رنگهای مختلفی استفاده شود. در این مرحله لایه رنگ بهطور یکنواخت روی سطح سوله پاشیده میشود. بسته به نوع رنگ انتخابی این لایه ممکن است با دستگاههای اسپری یا روشهای غلتکی اعمال شود.
رنگهای صنعتی که در این مرحله استفاده میشوند معمولاً مقاوم در برابر سایش خوردگی و شرایط جوی مختلف هستند. انتخاب رنگ بستگی به عواملی چون شرایط محیطی نوع فلز و کاربری سوله دارد. در این مرحله لایه رنگی باید بهگونهای اعمال شود که سطحی صاف و یکدست به وجود آید.
تکرار لایهها: بهبود پوشش و مقاومت
در بسیاری از موارد برای ایجاد یک پوشش مقاوم و با دوام باید چندین لایه رنگ به طور پیوسته روی سطح سوله اعمال شود. تعداد لایهها بستگی به نوع رنگ شرایط محیطی و ضخامت مورد نظر دارد. هر لایه جدید که بر روی لایه قبلی زده میشود موجب افزایش مقاومت در برابر آسیبهای خارجی افزایش دوام رنگ و افزایش پوششدهی میشود.
برای حصول نتیجه بهتر باید هر لایه رنگ بهطور کامل خشک شود و سپس لایه بعدی اعمال گردد. در غیر این صورت ممکن است رنگهای مختلف به درستی به هم پیوند نخورند و کیفیت نهایی به خطر بیفتد. برخی از رنگها نیاز به خشک شدن طبیعی دارند در حالی که برخی دیگر ممکن است به خشککردن سریعتر نیاز داشته باشند.
عوامل مؤثر بر ضخامت رنگ در سولهها: ترکیبی از علم و تجربه
نوع رنگ: هر رنگ ویژگیهای خاص خود را دارد و ضخامت بهینه برای آن نیز متفاوت خواهد بود. رنگهای اپوکسی پلیاورتان و آکریلیک با توجه به ترکیبات شیمیایی و ویژگیهای فنی خود نیاز به ضخامتهای مختلف دارند. به طور مثال رنگهای اپوکسی به دلیل مقاومت بالای خود در برابر مواد شیمیایی و سایش معمولاً نیاز به لایههای ضخیمتری دارند در حالی که رنگهای آکریلیک بیشتر برای ظاهر و مقاومت در برابر اشعه ماوراء بنفش استفاده میشوند و ضخامت کمتری نیاز دارند.
نوع فلز: نوع فلزی که برای ساخت سوله به کار رفته است تأثیر زیادی بر ضخامت رنگ دارد. فلزاتی مانند آهن و فولاد معمولاً به لایههای ضخیمتری از رنگ نیاز دارند زیرا این فلزات در معرض زنگزدگی قرار دارند. در مقابل آلومینیوم که نسبت به سایر فلزات مقاومتر در برابر خوردگی است ممکن است به ضخامت کمتری از رنگ نیاز داشته باشد اما همچنان باید از رنگهای مقاوم در برابر شرایط جوی استفاده شود.
ضخامت معمول برای رنگهای سوله: راهنمایی برای پروژههای مختلف
ضخامت رنگ باید بر اساس شرایط خاص هر سوله و محیط آن تنظیم شود. در اینجا یک راهنمای عمومی برای ضخامت رنگ در انواع مختلف محیطها ارائه میدهیم:
محیطهای معتدل (مانند مناطق با شرایط جوی معمول):
ضخامت کل: 40 میکرون
آستر: 20 میکرون
رویه: 20 میکرون
محیطهای سخت (محیطهای صنعتی یا مناطق با رطوبت بالا و آلایندههای شیمیایی):
ضخامت کل: 60 تا 120 میکرون
آستر: 30 تا 60 میکرون
لایه میانی: 30 تا 60 میکرون
رویه: 30 تا 60 میکرون
این اعداد تنها بهعنوان یک راهنمای اولیه ارائه میشوند و ضخامت دقیق باید بر اساس شرایط پروژه نوع رنگ و نوع فلز انتخاب شود.
اهمیت کنترل ضخامت رنگ: راز موفقیت پوشش رنگی
رعایت دقیق ضخامت رنگ برای کارایی و دوام آن ضروری است. اگر ضخامت رنگ کمتر از حد لازم باشد پوشش محافظتی به درستی عمل نمیکند و فلز در معرض آسیبهایی همچون خوردگی و سایش قرار خواهد گرفت. این امر ممکن است باعث کاهش عمر سازه و افزایش هزینههای نگهداری شود.
از سوی دیگر اگر ضخامت رنگ بیش از حد باشد این میتواند مشکلاتی نظیر ترکخوردگی رنگ و کاهش چسبندگی آن ایجاد کند. رنگ اضافی ممکن است باعث شود که لایهها نتوانند به درستی به سطح فلز بچسبند که در نهایت منجر به شکستگی و آسیبهای بیشتر خواهد شد.
روشهای اندازهگیری ضخامت رنگ: دقت در اندازهگیری کلید موفقیت
برای اطمینان از اعمال ضخامت صحیح رنگ باید از ابزارهای اندازهگیری دقیق استفاده کرد. دو روش معمول برای اندازهگیری ضخامت رنگ عبارتند از:
دستگاه اندازهگیری ضخامت رنگ: این دستگاهها از تکنولوژیهای مختلفی مانند مغناطیسی یا گردابی برای اندازهگیری دقیق ضخامت رنگ استفاده میکنند. این روش بسیار سریع و دقیق است و امکان اندازهگیری در چندین نقطه از سطح را فراهم میآورد.
نتیجهگیری: رنگآمیزی سولهها که نوعی سازه فلزی پیشساخته هستند به این دلیل که پاسخ مناسبی به سؤال سوله ارزان و کاربردهای متنوع آن در صنایع انبارها سالنهای ورزشی و غیره میدهد اهمیت ویژهای دارد. این رنگآمیزی نه تنها بر زیبایی تأثیر میگذارد بلکه یک اقدام ضروری برای حفظ کیفیت دوام و عملکرد بهینه آنها در طول زمان است. اهمیت این مرحله در فرآیند نگهداری آن را به یکی از اصلیترین راهکارها برای مقابله با عوامل مخرب محیطی تبدیل کرده است.