وای فوم پیشرو در تولید انواع فوم لاستیک صنعتی
شرکت وای فوم به عنوان یکی از مجموعه های فعال در عرصه تولید فوم لاستیک صنعتی در ایران با بهره گیری از دانش فنی و ماشین آلات به روز طیف وسیعی از محصولات فومی و لاستیکی را برای کاربردهای متنوع صنعتی تولید و عرضه می کند. فوم لاستیک صنعتی ماده ای الاستومری است که با ایجاد ساختاری سلولی حاوی حباب های گاز درون ماتریس پلیمری تولید می شود و به دلیل ویژگی های منحصر به فرد خود مانند سبکی وزن انعطاف پذیری جذب ضربه عایق بندی حرارتی و صوتی و مقاومت در برابر شرایط محیطی نقشی حیاتی در صنایع مختلف ایفا می کند. تولید این فوم ها یک فرآیند مهندسی پیچیده است که نیازمند کنترل دقیق بر مواد اولیه فرمولاسیون و پارامترهای فرآیندی است تا محصول نهایی با خواص مورد انتظار تولید شود.
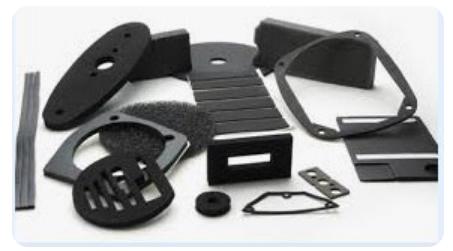
تعریف فنی و عملکرد فوم لاستیک صنعتی
فوم لاستیک صنعتی یا لاستیک سلولی (Cellular Rubber) به ماده ای پلیمری اطلاق می شود که ساختار آن متشکل از یک ماتریس الاستومری (مانند EPDM NBR نئوپرن سیلیکون) و تعداد زیادی سلول یا حباب گاز پراکنده در آن است. این ساختار سلولی عامل اصلی خواص ویژه این فوم ها مانند چگالی پایین (معمولاً بین ۰.۰۲ تا ۰.۳ گرم بر سانتی متر مکعب) تراکم پذیری بالا ارتجاعیت و قابلیت جذب انرژی است. عملکرد اصلی فوم لاستیک صنعتی بر پایه همین خواص استوار است. این مواد به عنوان درزگیر (Sealing) برای جلوگیری از نفوذ مایعات و گازها بالشتک (Cushioning) برای جذب ضربه و ارتعاش و عایق (Insulation) حرارتی و صوتی به کار می روند. بسته به نوع الاستومر پایه و ساختار سلولی (سلول-باز یا سلول-بسته) عملکرد و کاربرد فوم متفاوت خواهد بود. فوم های سلول-بسته به دلیل عدم ارتباط بین سلول ها مقاومت بالایی در برابر نفوذ آب و هوا دارند و برای کاربردهای درزگیری و آب بندی ایده آل هستند. در مقابل فوم های سلول-باز به دلیل ارتباط بین سلول ها قابلیت جذب صوت و عبور هوا را دارند و در کاربردهای آکوستیک و فیلتراسیون استفاده می شوند.
اجزای اصلی و اصول کارکرد فرآیند تولید
فرآیند تولید فوم لاستیک صنعتی یک عملیات چند مرحله ای مهندسی شیمی و پلیمر است که شامل اجزای اصلی و مراحل کلیدی زیر می باشد :
- مواد اولیه (Raw Materials) :
- الاستومر پایه : انتخاب نوع الاستومر (مانند EPDM NBR SBR CR (نئوپرن) سیلیکون) بر اساس خواص مورد نیاز محصول نهایی (مقاومت دمایی مقاومت شیمیایی مقاومت در برابر ازن و UV و غیره) صورت می گیرد.
- عامل پف زا (Blowing Agent) : ماده ای شیمیایی یا فیزیکی که تحت شرایط خاص (معمولاً حرارت) تجزیه شده یا تغییر فاز داده و گاز (مانند نیتروژن دی اکسید کربن) آزاد می کند. این گاز باعث ایجاد ساختار سلولی و انبساط لاستیک می شود. عوامل شیمیایی رایج شامل آزودی کربونامید (ADC) و OBSH هستند. عوامل فیزیکی شامل گازهای بی اثر یا مایعات فرار می باشند.
- عامل پخت یا ولکانیزاسیون (Curing/Vulcanizing Agent) : موادی مانند گوگرد یا پراکسیدها که با ایجاد اتصالات عرضی (Cross-linking) بین زنجیره های پلیمری باعث افزایش استحکام ارتجاعیت و پایداری ابعادی لاستیک می شوند.
- فعال کننده ها و شتاب دهنده ها (Activators/Accelerators) : ترکیباتی که سرعت واکنش ولکانیزاسیون را افزایش داده و دمای مورد نیاز آن را کاهش می دهند (مانند اکسید روی و اسید استئاریک به عنوان فعال کننده و تیازول ها یا سولفنامیدها به عنوان شتاب دهنده).
- پرکننده ها (Fillers) : موادی مانند کربن سیاه (Carbon Black) یا سیلیکا که برای بهبود خواص مکانیکی (مانند مقاومت سایشی و استحکام کششی) و کاهش هزینه به فرمولاسیون اضافه می شوند.
- نرم کننده ها (Plasticizers) : روغن ها یا استرها که برای افزایش انعطاف پذیری و بهبود فرآیندپذیری کامپاند به کار می روند.
- افزودنی های دیگر : شامل آنتی اکسیدان ها آنتی ازونانت ها رنگدانه ها و عوامل ضد شعله برای بهبود خواص خاص.
- اصول کارکرد فرآیند تولید :
- مخلوط سازی (Mixing/Compounding) : تمامی مواد اولیه طبق فرمولاسیون دقیق در میکسرهای داخلی (مانند بنبوری) یا بر روی غلتک های دوار (Two-roll mill) تحت دما و زمان کنترل شده با یکدیگر مخلوط می شوند تا یک کامپاند همگن حاصل شود.
- شکل دهی (Shaping) : کامپاند همگن به شکل مورد نظر (ورق نوار پروفیل) از طریق فرآیندهایی مانند اکستروژن (Extrusion) یا کلندرینگ (Calendering) در می آید. برای قطعات با اشکال پیچیده از قالب گیری فشاری (Compression Molding) یا تزریقی (Injection Molding) استفاده می شود.
- فوم زایی و پخت (Foaming and Curing) : مرحله کلیدی که در آن محصول شکل دهی شده تحت حرارت معین قرار می گیرد. در این دما عامل پف زا تجزیه شده و گاز آزاد می کند که باعث انبساط کامپاند و تشکیل ساختار سلولی می شود. همزمان یا بلافاصله پس از آن واکنش ولکانیزاسیون رخ می دهد که ساختار لاستیک را پایدار کرده و خواص نهایی را ایجاد می کند. کنترل دقیق دما و زمان در این مرحله برای دستیابی به چگالی و ساختار سلولی مطلوب حیاتی است. فرآیندهای مدرن مانند ولکانیزاسیون با امواج مایکروویو (Microwave Vulcanization) می توانند سرعت پخت را افزایش دهند.
- خنک سازی و عملیات تکمیلی (Cooling and Finishing) : محصول فوم شده و پخت شده به آرامی خنک می شود تا از تغییر شکل ناخواسته جلوگیری شود. سپس عملیات تکمیلی مانند برش (Cutting) شیارزنی (Slitting) چسب زنی (Adhesive application) یا لمینت با مواد دیگر انجام می شود.
انواع فوم های لاستیکی صنعتی و ویژگی های آن ها
فوم های لاستیک صنعتی بر اساس نوع الاستومر پایه و ساختار سلولی طبقه بندی می شوند. هر نوع دارای ویژگی ها و کاربردهای خاص خود است :
- فوم EPDM (Ethylene Propylene Diene Monomer) :
- ویژگی ها : مقاومت عالی در برابر شرایط جوی نور خورشید (UV) ازن آب و بخار. انعطاف پذیری خوب در دماهای پایین و بالا (معمولاً ۴۰- تا ۱۵۰+ درجه سانتی گراد). عایق الکتریکی خوب.
- ساختار سلولی : عمدتاً سلول-بسته تولید می شود که مقاومت آن را در برابر نفوذ آب افزایش می دهد.
- کاربردها : درزگیرهای خودرو (درب پنجره صندوق) شیلنگ ها عایق بندی ساختمان (پروفیل های در و پنجره) سیستم های HVAC کاربردهای بیرونی.
- فوم NBR (Nitrile Butadiene Rubber) :
- ویژگی ها : مقاومت عالی در برابر روغن ها سوخت ها گریس ها و حلال های هیدروکربنی. مقاومت سایشی خوب.
- ساختار سلولی : به صورت سلول-بسته و سلول-باز موجود است. نوع سلول-بسته برای آب بندی در محیط های روغنی مناسب است.
- کاربردها : واشرها و درزگیرهای صنعتی در معرض روغن قطعات خودرو (سیستم سوخت) شیلنگ های صنعتی لایه های محافظ.
- فوم نئوپرن (Neoprene / CR – Chloroprene Rubber) :
- ویژگی ها : تعادل خوب بین خواص مختلف؛ مقاومت متوسط در برابر روغن مواد شیمیایی ازن شعله و شرایط جوی. استحکام مکانیکی و مقاومت سایشی خوب.
- ساختار سلولی : عمدتاً سلول-بسته.
- کاربردها : کاربردهای عمومی صنعتی درزگیرها واشرها لباس های غواصی عایق های الکتریکی قطعات خودرو کاربردهای دریایی.
- فوم SBR (Styrene Butadiene Rubber) :
- ویژگی ها : مقاومت سایشی خوب استحکام کششی مناسب هزینه نسبتاً پایین. مقاومت ضعیف تر در برابر ازن UV و روغن نسبت به EPDM یا نئوپرن.
- ساختار سلولی : می تواند سلول-بسته یا سلول-باز باشد. اغلب با الاستومرهای دیگر مانند CR یا EPDM ترکیب می شود تا هزینه را کاهش داده و فرآیندپذیری را بهبود بخشد.
- کاربردها : واشرهای کم هزینه لایه های ضربه گیر برخی قطعات صنعتی عمومی.
- فوم سیلیکون (Silicone Foam) :
- ویژگی ها : مقاومت عالی در برابر دماهای بسیار بالا و پایین (معمولاً ۶۰- تا ۲۰۰+ درجه سانتی گراد و حتی بالاتر). مقاومت خوب در برابر UV ازن و شرایط جوی. زیست سازگاری خوب (در گریدهای خاص). مقاومت پایین در برابر سایش و پارگی نسبت به سایر الاستومرها.
- ساختار سلولی : سلول-بسته و سلول-باز موجود است.
- کاربردها : درزگیرها و واشرهای دما بالا صنایع غذایی و پزشکی (گریدهای خاص) عایق های حرارتی و الکتریکی صنایع هوافضا و الکترونیک.
- فوم لاستیک طبیعی (Natural Rubber Foam – Latex Foam) :
- ویژگی ها : ارتجاعیت و مقاومت فشاری (Compression Set) عالی. مقاومت پارگی بالا. انعطاف پذیری خوب در دمای پایین. مقاومت ضعیف در برابر ازن UV روغن ها و دماهای بالا.
- ساختار سلولی : عمدتاً سلول-باز (تولید شده با فرآیندهای Dunlop یا Talalay).
- کاربردها : تشک و بالش مبلمان لایه های زیرین فرش بالشتک های ضربه گیر.
شرکت هایی مانند وای فوم معمولاً طیف وسیعی از این فوم ها را بر اساس نیاز مشتری و کاربردهای خاص تولید می کنند.
کاربردهای صنعتی گسترده فوم لاستیک
فوم لاستیک صنعتی به دلیل تطبیق پذیری و خواص منحصربه فرد در طیف وسیعی از صنایع کاربرد دارد :
- صنعت خودرو : یکی از بزرگترین مصرف کنندگان فوم لاستیک. کاربردها شامل :
- درزگیرها و آب بندها : برای درب ها پنجره ها صندوق عقب سانروف و چراغ ها جهت جلوگیری از نفوذ آب هوا و گرد و غبار (عمدتاً EPDM و نئوپرن سلول-بسته).
- عایق صدا و لرزش (NVH – Noise, Vibration, Harshness) : استفاده در داشبورد کف خودرو سقف و محفظه موتور برای کاهش صدا و ارتعاشات (فوم های EPDM PU سلول-باز و سلول-بسته).
- واشرها (Gaskets) : در موتور گیربکس و سایر اجزاء برای آب بندی روغن و مایعات (عمدتاً NBR و سیلیکون).
- بالشتک ها و ضربه گیرها : در صندلی ها زیرآرنجی ها و سیستم تعلیق.
- صنعت ساختمان و ساخت وساز :
- عایق بندی حرارتی و صوتی : عایق لوله های تأسیسات (HVAC) درزگیر پنجره ها و درب ها نوارهای انبساط (Expansion joints). فوم های EPDM و الاستومری (Elastomeric foams) رایج هستند.
- آب بندی : درزگیری سقف ها فونداسیون ها و اتصالات ساختمانی.
- سیستم های تهویه مطبوع (HVAC) :
- عایق بندی لوله ها و کانال ها : برای جلوگیری از اتلاف حرارت یا سرما و کنترل چگالش (فوم های EPDM NBR پلی اتیلن).
- درزگیرها و واشرها : برای اتصالات و دریچه ها.
- لرزه گیرها : برای کاهش ارتعاشات تجهیزات.
- صنعت الکترونیک :
- واشرهای آب بندی : برای محافظت از قطعات حساس در برابر رطوبت و گرد و غبار (IP rating).
- بالشتک های ضربه گیر : برای محافظت از اجزای ظریف.
- عایق های الکتریکی و حرارتی.
- واشرهای محافظ EMI/RFI : (در صورت استفاده از پرکننده های رسانا).
- تجهیزات صنعتی و ماشین آلات :
- واشرها و درزگیرها : برای آب بندی سیالات و گازها در پمپ ها کمپرسورها و ماشین آلات.
- پدهای ضد لرزش : برای جداسازی ارتعاشات ماشین آلات.
- لایه های محافظ و ضربه گیر.
- بسته بندی :
- محافظت از کالاهای شکننده : استفاده به عنوان ضربه گیر در بسته بندی تجهیزات حساس الکترونیکی پزشکی و شیشه ای (فوم های پلی اتیلن و پلی یورتان نیز رایج هستند اما فوم لاستیک برای کاربردهای خاص و نیازمند ارتجاعیت بالا استفاده می شود).
- تجهیزات ورزشی و پزشکی :
- لایه های نرم و ضربه گیر : در کلاه های ایمنی زانوبندها مت های یوگا (فوم EVA و لاستیک).
- ارتزها و پروتزها : بالشتک های طبی و اجزای ارتوپدی (گریدهای زیست سازگار مانند سیلیکون).
استانداردهای بین المللی و کنترل کیفیت
تولید فوم لاستیک صنعتی با کیفیت و عملکرد قابل اطمینان نیازمند رعایت دقیق استانداردهای بین المللی و اجرای فرآیندهای کنترل کیفیت (QC) جامع است. این استانداردها زبان مشترکی برای تولیدکنندگان و مصرف کنندگان فراهم می کنند و حداقل الزامات عملکردی را تعریف می نمایند.
- استانداردهای کلیدی :
- ASTM D۱۰۵۶ (Standard Specification for Flexible Cellular Materials—Sponge or Expanded Rubber) : یکی از پرکاربردترین استانداردها در آمریکای شمالی. این استاندارد فوم های لاستیکی را بر اساس نوع (Type) کلاس (Class) و گرید (Grade) طبقه بندی می کند :
- Type ۱ : سلول-باز (Open-cell)
- Type ۲ : سلول-بسته (Closed-cell)
- Class : مقاومت در برابر روغن و دما (A تا D)
- Grade : مقاومت فشاری (Compression Deflection) یا سختی (Hardness) و الزامات آزمون های فیزیکی دیگر مانند مقاومت فشاری ماندگار (Compression Set) مقاومت حرارتی و مقاومت در برابر دمای پایین. مثال : ۲C۳ نشان دهنده فوم سلول-بسته (Type ۲) مقاومت متوسط در برابر روغن (Class C) و گرید سختی ۳ است.
- ISO Standards : سازمان بین المللی استانداردسازی (ISO) نیز استانداردهای متعددی برای مواد سلولی انعطاف پذیر دارد از جمله :
- ISO ۱۷۹۸ : تعیین خواص کششی (استحکام کششی و ازدیاد طول تا پارگی).
- ISO ۱۸۵۶ : تعیین مقاومت فشاری ماندگار (Compression Set).
- ISO ۲۴۳۹ : تعیین سختی (روش فرورفتگی).
- ISO ۳۳۸۶ : تعیین خواص تنش-کرنش فشاری.
- ISO ۴۸ : تعیین سختی (شور A و OO).
- استانداردهای صنعتی خاص : صنایعی مانند خودرو (مانند استانداردهای FMVSS ۳۰۲ برای اشتعال پذیری) هوافضا (BMS) و راه آهن استانداردهای خاص خود را دارند که تولیدکنندگان باید رعایت کنند.
- پارامترهای کنترل کیفیت :
- چگالی (Density) : اندازه گیری وزن به ازای حجم نشان دهنده میزان انبساط فوم.
- سختی (Hardness) : مقاومت در برابر فرورفتگی معمولاً با دستگاه های Shore A یا Shore OO اندازه گیری می شود.
- مقاومت فشاری (Compression Deflection – CFD) : نیروی لازم برای فشرده کردن فوم به درصد مشخصی از ضخامت اولیه (معمولاً ۲۵%).
- مقاومت فشاری ماندگار (Compression Set) : درصد تغییر شکل دائمی فوم پس از قرار گرفتن تحت فشار برای مدت زمان و دمای مشخص. این پارامتر برای کاربردهای درزگیری بسیار مهم است.
- استحکام کششی و ازدیاد طول تا پارگی (Tensile Strength & Elongation at Break) : مقاومت فوم در برابر کشش و میزان کشیدگی قبل از پاره شدن.
- مقاومت پارگی (Tear Strength) : مقاومت در برابر انتشار پارگی.
- جذب آب (Water Absorption) : میزان جذب آب توسط فوم سلول-بسته (باید بسیار کم باشد).
- یکنواختی ساختار سلولی (Cell Structure Uniformity) : بررسی اندازه و توزیع سلول ها با میکروسکوپ.
- پایداری ابعادی (Dimensional Stability) : مقاومت در برابر تغییر ابعاد (جمع شدگی یا انبساط) در دماهای مختلف.
- آزمون های مقاومت محیطی : مقاومت در برابر روغن ازن UV دماهای بالا و پایین مواد شیمیایی و شعله (در صورت نیاز).
تولیدکنندگانی مانند وای فوم با پیاده سازی سیستم های مدیریت کیفیت (مانند ISO ۹۰۰۱) و انجام آزمون های دقیق در مراحل مختلف تولید (از مواد اولیه تا محصول نهایی) انطباق محصولات خود با این استانداردها و نیازهای مشتری را تضمین می کنند.
فناوری های پیشرفته در تولید فوم لاستیک
صنعت فوم لاستیک به طور مداوم در حال تکامل است و فناوری های پیشرفته با هدف بهبود خواص محصول افزایش بهره وری تولید کاهش هزینه ها و رعایت الزامات زیست محیطی در حال توسعه و به کارگیری هستند :
- عوامل پف زای پیشرفته :
- عوامل دوستدار محیط زیست : جایگزینی عوامل پف زای سنتی که ممکن است ترکیبات مضری آزاد کنند (مانند برخی آمین ها) با گزینه های سازگارتر با محیط زیست مانند CO۲ سوپرکریتیکال آب یا عوامل شیمیایی با محصولات جانبی بی خطر.
- عوامل پف زای میکروانکپسوله : کپسول های حاوی عامل پف زا که در دمای دقیق تری آزاد می شوند و کنترل بهتری بر اندازه و توزیع سلول ها فراهم می کنند.
- کنترل فرآیند و اتوماسیون :
- سیستم های مانیتورینگ آنلاین : استفاده از سنسورها برای کنترل لحظه ای پارامترهای کلیدی مانند دما فشار و سرعت در خطوط اکستروژن و پخت.
- اتوماسیون : استفاده از ربات ها و سیستم های کنترل پیشرفته برای افزایش دقت و تکرارپذیری در مراحل مخلوط سازی شکل دهی و برش و کاهش دخالت نیروی انسانی.
- علوم مواد و فرمولاسیون :
- نانوکامپوزیت ها : استفاده از نانوذرات (مانند نانوکلی نانولوله های کربنی گرافن) به عنوان پرکننده برای بهبود چشمگیر خواص مکانیکی حرارتی و الکتریکی فوم با درصدهای وزنی بسیار کم.
- آلیاژهای پلیمری و ترکیبات ویژه : ترکیب الاستومرهای مختلف (مانند آلیاژ NBR/PVC) برای دستیابی به ترکیبی از خواص مطلوب مانند مقاومت همزمان در برابر روغن و ازن. توسعه فرمولاسیون های خاص برای کاربردهای ویژه مانند فوم های رسانا (Conductive) ضد الکتریسیته ساکن (Anti-static) یا با مقاومت بسیار بالا در برابر شعله.
- تکنیک های تولید نوین :
- ولکانیزاسیون با مایکروویو یا هوای داغ (HAV) : فرآیندهای پخت سریع تر و کارآمدتر انرژی نسبت به پخت با بخار سنتی به ویژه برای پروفیل های اکسترود شده.
- خطوط تولید پیوسته (Continuous Production Lines) : افزایش بهره وری و یکنواختی محصول در مقایسه با فرآیندهای بچ.
- چاپ سه بعدی (۳D Printing) : اگرچه هنوز در مراحل اولیه برای فوم لاستیک است اما پتانسیل تولید قطعات با هندسه های پیچیده و سفارشی را دارد.
- پایداری و اقتصاد چرخشی :
- استفاده از مواد بازیافتی : به کارگیری لاستیک بازیافتی (مانند پودر تایر) در فرمولاسیون برای کاهش مصرف مواد اولیه و کاهش ضایعات.
- الاستومرهای زیست پایه (Bio-based Elastomers) : تحقیق و توسعه بر روی الاستومرهایی که از منابع تجدیدپذیر (مانند روغن های گیاهی) مشتق شده اند.
شرکت های پیشرو مانند وای فوم با سرمایه گذاری در تحقیق و توسعه (R&D) و اتخاذ این فناوری ها تلاش می کنند تا محصولاتی با عملکرد بهتر هزینه کمتر و سازگاری بیشتر با محیط زیست ارائه دهند.
چالش ها و محدودیت های فنی در صنعت فوم لاستیک
علی رغم پیشرفت ها تولید و استفاده از فوم لاستیک صنعتی با چالش ها و محدودیت های فنی متعددی روبرو است :
- یکنواختی ساختار سلولی و چگالی : دستیابی به توزیع کاملاً یکنواخت اندازه سلول ها و چگالی در سراسر محصول به ویژه در قطعات ضخیم یا با هندسه پیچیده دشوار است. عدم یکنواختی می تواند منجر به تغییرات خواص مکانیکی و عملکردی در نقاط مختلف شود.
- کنترل دقیق فرآیند : فرآیند فوم زایی و پخت به پارامترهایی مانند دما فشار و زمان بسیار حساس است. تغییرات جزئی می تواند منجر به محصول خارج از مشخصات (Off-spec) شود. کنترل دقیق این پارامترها در مقیاس صنعتی چالش برانگیز است.
- مقاومت فشاری ماندگار (Compression Set) : اگرچه بسیاری از فوم های لاستیک ارتجاعیت خوبی دارند اما تحت فشار مداوم و به ویژه در دماهای بالا ممکن است دچار تغییر شکل دائمی شوند. بهبود این خاصیت برای کاربردهای درزگیری حیاتی است و یک چالش فرمولاسیونی محسوب می شود.
- پایداری ابعادی : برخی فوم ها ممکن است پس از تولید دچار جمع شدگی (Shrinkage) یا انبساط (Expansion) شوند که می تواند در کاربردهایی با تلرانس های ابعادی دقیق مشکل ساز باشد.
- محدودیت های دمایی و شیمیایی : هر نوع الاستومر دارای محدودیت های دمایی و مقاومت شیمیایی خاص خود است. دستیابی به فومی که همزمان در برابر دماهای بسیار بالا مواد شیمیایی خورنده و روغن ها مقاوم باشد بسیار دشوار و پرهزینه است.
- قابلیت اشتعال پذیری : بسیاری از الاستومرها ذاتاً قابل اشتعال هستند. افزودن مواد ضد شعله برای برآورده کردن استانداردهای ایمنی (مانند FMVSS ۳۰۲ در خودرو) می تواند بر خواص مکانیکی فرآیندپذیری و هزینه تأثیر منفی بگذارد.
- چالش های زیست محیطی و بازیافت : برخی عوامل پف زا یا افزودنی های قدیمی ممکن است ملاحظات زیست محیطی داشته باشند. همچنین بازیافت فوم لاستیک به دلیل ساختار سلولی و اتصالات عرضی (در لاستیک های ولکانیزه شده) پیچیده و پرهزینه است. توسعه روش های بازیافت مؤثر و استفاده از مواد پایدار همچنان یک چالش است.
- هزینه : فوم های لاستیک با کارایی بالا (High-performance) مانند سیلیکون یا فوم های با افزودنی های خاص می توانند گران باشند. ایجاد تعادل بین عملکرد مورد نیاز و هزینه تولید یک چالش دائمی است.
نکات کلیدی برای بهینه سازی و بهبود عملکرد
برای غلبه بر چالش ها و دستیابی به فوم لاستیک صنعتی با عملکرد بهینه توجه به نکات کلیدی زیر ضروری است :
- انتخاب دقیق مواد اولیه : کلید دستیابی به خواص مطلوب انتخاب هوشمندانه الاستومر پایه نوع و مقدار عامل پف زا سیستم پخت پرکننده ها و افزودنی ها بر اساس الزامات کاربرد نهایی است.
- بهینه سازی فرمولاسیون : استفاده از طراحی آزمایش ها (DOE – Design of Experiments) و مدل سازی برای یافتن ترکیب بهینه مواد اولیه که تعادل مناسبی بین خواص مختلف (مانند سختی مقاومت فشاری ماندگار چگالی مقاومت حرارتی و شیمیایی) برقرار کند.
- کنترل دقیق پارامترهای فرآیندی : تنظیم و کنترل دقیق دما فشار زمان مخلوط سازی سرعت اکستروژن پروفیل دمایی پخت و سرعت خنک سازی برای اطمینان از یکنواختی ساختار سلولی و خواص محصول.
- بهبود فرآیند مخلوط سازی : اطمینان از پراکندگی یکنواخت تمام اجزا به ویژه عامل پف زا و عوامل پخت در ماتریس الاستومری برای جلوگیری از ایجاد نقاط ضعف یا فوم زایی نامنظم.
- طراحی قالب و ابزار : طراحی مناسب قالب ها و دای های اکستروژن برای دستیابی به شکل و ابعاد دقیق محصول نهایی و جلوگیری از ایجاد تنش های داخلی یا نقص در فوم.
- کنترل کیفیت جامع : پیاده سازی یک برنامه کنترل کیفیت دقیق شامل بازرسی مواد اولیه نظارت بر فرآیند و انجام آزمون های استاندارد بر روی محصول نهایی برای اطمینان از انطباق با مشخصات. استفاده از داده های QC برای تنظیم و بهبود مستمر فرآیند.
- درک عمیق اندرکنش مواد و فرآیند : مطالعه و تحقیق برای درک بهتر چگونگی تأثیر متقابل مواد اولیه و پارامترهای فرآیندی بر ساختار سلولی نهایی و خواص فوم.
- همکاری با مشتریان : تعامل نزدیک با مصرف کنندگان نهایی برای درک دقیق نیازها و الزامات کاربردی آنها و توسعه راه حل های فومی سفارشی.
با تمرکز بر این نکات تولیدکنندگان فوم لاستیک مانند وای فوم می توانند محصولاتی با کیفیت بالاتر عملکرد بهتر و قابلیت اطمینان بیشتر تولید کنند.
نتیجه گیری علمی و تخصصی
فوم لاستیک صنعتی به عنوان دسته ای از مواد مهندسی پیشرفته نقشی حیاتی در فناوری مدرن ایفا می کند. تولید موفقیت آمیز این مواد مستلزم درک عمیق اصول علم پلیمر مهندسی شیمی و مکانیک مواد است. کنترل دقیق بر ساختار سلولی (اندازه توزیع اتصال سلول ها) و انتخاب هوشمندانه الاستومر پایه و افزودنی ها امکان تنظیم دقیق خواص ماکروسکوپی مانند چگالی سختی مقاومت فشاری ماندگار عایق بندی حرارتی/صوتی و مقاومت محیطی را فراهم می آورد. چالش هایی نظیر یکنواختی محصول پایداری ابعادی بهبود مقاومت فشاری ماندگار و ملاحظات زیست محیطی محرک اصلی نوآوری در این صنعت هستند. ظهور فناوری هایی مانند نانوکامپوزیت ها عوامل پف زای پیشرفته و اتوماسیون فرآیند چشم انداز تولید فوم هایی با کارایی بالاتر و پایدارتر را ترسیم می کند. شرکت هایی که قادر به تسلط بر پیچیدگی های فرمولاسیون و فرآیند تولید هستند و استانداردهای کیفی دقیق را رعایت می کنند مانند وای فوم می توانند در این بازار رقابتی راه حل های مؤثری برای نیازهای متنوع صنعتی ارائه دهند. آینده این صنعت به سمت توسعه مواد پایدارتر فرآیندهای کارآمدتر و فوم هایی با عملکردهای چندگانه و هوشمند پیش می رود.
پرسش و پاسخ
۱. تفاوت اصلی بین فوم لاستیک سلول-باز و سلول-بسته چیست؟
تفاوت اصلی در ساختار فیزیکی سلول ها نهفته است. در فوم لاستیک سلول-بسته (Closed-cell) هر سلول گازی توسط دیواره های پلیمری کاملاً محصور شده و از سلول های مجاور جدا است. این ساختار مانع از نفوذ آسان مایعات و گازها می شود و به همین دلیل این نوع فوم ها ضد آب هستند و به عنوان درزگیر و عایق حرارتی عملکرد عالی دارند. در مقابل در فوم لاستیک سلول-باز (Open-cell) سلول ها به یکدیگر متصل هستند و مسیری برای عبور هوا و مایعات ایجاد می کنند. این ساختار باعث می شود فوم نرم تر انعطاف پذیرتر و قابلیت جذب صوت بهتری داشته باشد اما مقاومت کمتری در برابر نفوذ آب دارد. کاربردهای اصلی آن شامل بالشتک ها فیلترها و عایق های صوتی است.
۲. کدام نوع فوم لاستیک برای کاربردهای بیرونی و در معرض شرایط جوی مناسب تر است؟
فوم EPDM (اتیلن پروپیلن دی ان مونومر) به طور کلی بهترین انتخاب برای کاربردهای بیرونی است. EPDM مقاومت فوق العاده ای در برابر عوامل مخرب محیطی مانند نور خورشید (UV) ازن رطوبت باران و تغییرات دمایی (هم گرما و هم سرما) از خود نشان می دهد. این ویژگی ها باعث می شود فوم EPDM به ویژه نوع سلول-بسته آن برای درزگیری پنجره ها درب ها پروفیل های ساختمانی قطعات خودرو که در معرض محیط بیرون هستند و سایر کاربردهای مشابه که نیاز به دوام طولانی مدت در شرایط جوی دارند ایده آل باشد. فوم نئوپرن نیز مقاومت خوبی در برابر شرایط جوی دارد اما مقاومت EPDM در برابر UV و ازن معمولاً برتر است.
۳. چگالی فوم لاستیک چگونه در فرآیند تولید کنترل می شود؟
چگالی فوم لاستیک عمدتاً توسط مقدار و نوع عامل پف زا (Blowing Agent) و شرایط فرآیندی (دما و فشار) کنترل می شود.
- مقدار عامل پف زا : افزایش مقدار عامل پف زا در فرمولاسیون منجر به تولید حجم بیشتری گاز در حین فرآیند می شود که باعث انبساط بیشتر لاستیک و در نتیجه کاهش چگالی فوم نهایی می گردد. کاهش مقدار عامل پف زا چگالی را افزایش می دهد.
- نوع عامل پف زا : عوامل پف زای مختلف در دماهای متفاوتی تجزیه می شوند و حجم های متفاوتی از گاز تولید می کنند. انتخاب عامل پف زا با دمای تجزیه مناسب و بازده گازی مشخص برای کنترل چگالی مهم است.
- شرایط فرآیندی : دما و فشار در مرحله فوم زایی و پخت تأثیر مستقیمی بر میزان انبساط گاز و تثبیت ساختار سلولی دارند. دمای بالاتر یا زمان پخت طولانی تر می تواند منجر به انبساط بیشتر (تا حدی) و چگالی کمتر شود اما کنترل دقیق برای جلوگیری از تخریب فوم یا کلاپس سلولی ضروری است. فشار خارجی اعمال شده در طی فرآیند (مثلاً در قالب گیری) نیز می تواند بر چگالی نهایی تأثیر بگذارد.
بنابراین با تنظیم دقیق فرمولاسیون (به ویژه مقدار عامل پف زا) و کنترل پارامترهای فرآیندی تولیدکنندگان می توانند فوم لاستیک با چگالی مورد نظر برای کاربردهای خاص تولید کنند.